Duty Cycles
Air compressors play a crucial role in various industrial, commercial, and even DIY applications. One of the most important factors to consider when selecting or operating an air compressor is its duty cycle. This key specification can make or break your system’s efficiency, performance, and longevity. In this blog post, we’ll cover everything you need to know about air compressor duty cycles, including how they work, why they matter, and how to optimize your system for better performance and savings.
What is an Air Compressor Duty Cycle?
At its core, the duty cycle of an air compressor refers to how long the compressor runs compared to how long it rests during a total cycle. For example, if a compressor has a duty cycle of 60%, it means it will run for 6 minutes and then rest for 4 minutes during a 10-minute cycle. Compressors with tanks operate in this "on-off" mode, while tankless models (like your lungs!) have a 100% duty cycle since they are always "on."
The duty cycle is also a measure of how much consistent pressure (PSI) and flow (CFM) the compressor provides. A compressor with a 100% duty cycle at 125 PSI and 25 CFM means it can supply that pressure and flow continuously without needing to rest.
Key Points to Understand About Duty Cycles
1. Types of Compressors and Duty Cycles
Different types of air compressors have different duty cycle capabilities:
Piston Compressors
These typically have lower duty cycles because they need cooling periods.
Rotary Screw Compressors
Designed for continuous run (100% duty cycle), they are ideal for industrial settings requiring constant airflow.
Scroll and Vane Compressors
These models also offer higher duty cycles, making them suitable for high-demand applications like HVAC or manufacturing.
2. Impact of Environmental Factors
The surrounding environment can influence a compressor’s duty cycle. For example, higher ambient temperatures can cause compressors to overheat faster, reducing the effective duty cycle. Humidity may affect the machine's internal components, requiring more frequent maintenance to sustain performance.
3. Maintenance and Duty Cycle
A compressor’s duty cycle directly impacts its maintenance schedule. Machines that are frequently overworked may require more frequent oil changes, cleaning, and part replacements. Keeping your compressor within its rated duty cycle reduces wear and tear, extending its lifespan.
4. Duty Cycle and Energy Efficiency
Compressors operating beyond their rated duty cycles consume more energy, leading to higher operating costs. Sizing the compressor correctly and ensuring it doesn’t exceed its duty cycle can significantly reduce energy usage, saving your business money in the long run.
5. Effects of Overloading Compressors
Running a compressor beyond its rated duty cycle can cause overheating, excessive wear, and permanent damage to internal components. Overloading reduces system reliability and may lead to costly repairs or even compressor failure.
6. Tanked vs. Tankless Compressors
Compressors with tanks have lower duty cycles because the tank provides a buffer for air storage, allowing the motor to rest. Tankless compressors, on the other hand, operate continuously (100% duty cycle), which makes them ideal for situations requiring consistent, uninterrupted airflow.
7. Cost vs. Performance Trade-offs
When selecting a compressor, it’s important to balance cost and performance. Compressors with higher duty cycles often come with a higher upfront cost, but they are typically more durable and energy-efficient in the long term. Investing in the right compressor can lead to significant savings over time.
8. Portable vs. Stationary Compressors
The duty cycle requirements for portable compressors, commonly used in service vehicles or job sites, differ from stationary compressors found in industrial plants. Portable models are typically designed for intermittent use, while stationary compressors are built for continuous operation.
9. Noise Levels and Duty Cycle
Duty cycle can impact noise levels in compressors. Compressors running near their duty cycle limit may operate more noisily due to strain on the motor. Continuous-duty compressors are often quieter because they are designed to handle constant operation more efficiently.
10. Customizing Compressors for Specific Duty Cycles
Some compressors can be customized to meet specific duty cycle demands. This involves selecting the right combination of motor, tank, and control system to suit particular industrial or commercial applications, ensuring you get optimal performance tailored to your needs.
Why Duty Cycle Matters: Sizing for Efficiency
Selecting the right compressor for your needs is crucial for ensuring proper operation and longevity. Understanding the duty cycle is especially important when sizing your compressor for the following reasons:
Prevents Over-Cycling
Choosing the correct duty cycle for your compressor helps avoid frequent cycling, which wears down parts and shortens its lifespan.
Improves Efficiency
Properly sizing your compressor for the right duty cycle reduces energy waste and can save significant amounts on electricity costs.
Reduces Maintenance Costs
Compressors that operate within their duty cycle need less maintenance and last longer, reducing your overall operational costs.
100% Duty Cycle vs. Continuous Run: What’s the Difference?
It’s important to note the difference between a 100% duty cycle and continuous run operation. A compressor with a 100% duty cycle can provide a constant CFM and PSI during use but may still need time to cool down. On the other hand, a continuous-run compressor (usually rotary-screw models) is designed to operate non-stop without overheating, idling only when not in use. Continuous-run compressors are essential for industries that require non-stop air supply, such as manufacturing or mining.
Final Thoughts: Optimize Your System for Performance and Savings
Understanding and managing the duty cycle of your air compressor is essential for ensuring it meets your operational needs, delivers consistent performance, and saves on energy and maintenance costs. Whether you're selecting a compressor for industrial applications or sizing a new system, keeping the duty cycle in mind will help you avoid over-cycling, prevent equipment damage, and boost overall efficiency.
If you're ready to optimize your compressed air system or learn more about the latest innovations in air compressor technology, reach out to our team of experts today! We’ll help you find the perfect compressor for your specific needs—whether you need a high-duty cycle for continuous operation or a portable model for intermittent use.
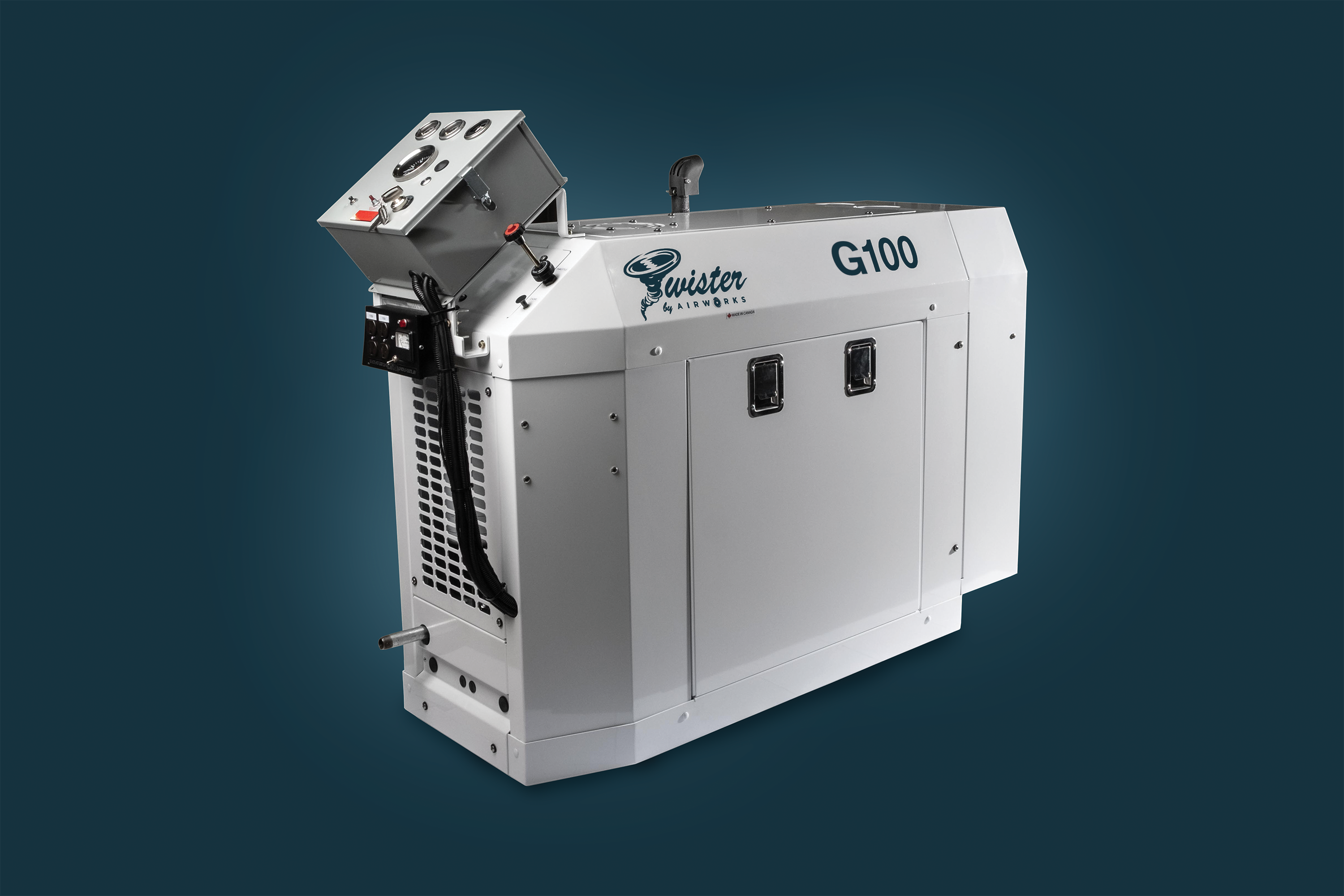
The Twister Series From Airworks Compressors Corp.
Every single model of Twister uses a rotary screw compressor, and is rated for a 100% duty cycle. Because each model is designed to operate continuously in the harshest conditions on the planet, you can rest assured that your maintenance schedule will be predictable, simple, and easy to manage.